
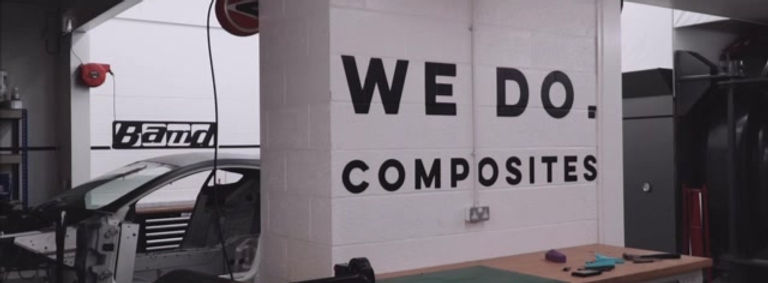
Current vacancies
“We're not interested in ego's, we're looking for genuine people, who take pride in their work and want to be part of an exciting growing team.”
- Adam Barmby, Chairman of BAMD ltd
We offer an exciting, fluid working environment and the opportunity to join our existing team of a skilled, experienced and positive people. With exciting Automotive and Motorsport contracts starting in 2020, the development and sustainable growth of our staff is of paramount importance to us and our continued business evolution.
All positions are Permanent, Salary is Dependent on experience, 42.5hr standard week + Overtime potential
-----------------------------------------------------------------------------------------------------------------------------------
Production Manager
Closing Date: 14th October 2024
Overview
BAMD Ltd are currently searching for an experienced and enthusiastic Production Manager to join our expanding team. The Production Manager is responsible for overseeing the production process to ensure that customer orders are fulfilled within pre-agreed deadlines and budgets. This role includes managing department supervisors, ensuring smooth workflow through different departments, planning capacity, and maintaining key customer and supplier relationships. Additionally, the Production Manager will be responsible for ensuring all necessary documentation and HR activities are carried out effectively. The role includes managing external sub-contractors and overseeing project-specific procurement until the Supply Chain element expands into a full-time position.
Key Responsibilities:
1. Leadership & Production Management: Lead and manage the production process to meet customer order deadlines and stay within budget. Oversee department supervisors/leaders to ensure production schedules are met. Plan and coordinate the movement of customer orders through various departments to ensure timely delivery.
2. Capacity Planning & Optimization: Ensure consistent workflow across departments, monitoring capacity to avoid bottlenecks. Communicate capacity issues (over/under) to the Senior Leadership Team for resolution. Optimize our multi-skilled Employees to drive production efficiency
3. HR & Appraisal Responsibilities: Conduct HR activities and appraisals for direct reports in line with company policies, supported by the HR & Communications Manager.
4. Documentation & Reporting: Issue, write, and manage documentation such as drawings, work orders, and sub-contractor purchase orders to ensure all departments have the information needed. Develop and implement a continuous improvement process through planned vs. actual reporting to identify inefficiencies and areas for improvement.
5. Customer Relations: Build and maintain positive relationships with customers post-sales handover to ensure transparent and trustworthy communication throughout the production process.
6. Team Engagement & Communication: Foster strong working relationships with production staff, ensuring any issues are heard and communicated to the Senior Leadership Team.
7. Organizational Discipline: Maintain professional organizational practices such as meetings, action points, calendar management, and effective use of communication tools like Microsoft Teams and email.
Additional Responsibilities (Supply Chain & Procurement):
1. External Sub-Contractor Management: Manage external production sub-contractors, ensuring they receive correct information and meet the company’s expectations.
2. Operations Consumable Management: Ensure the business has sufficient stock of manufacturing components, optimizing costs through bulk discounts and usage reports.
3. Project-Specific Procurement: Oversee procurement of project-specific materials, ensuring they meet cost, quality, and deadline requirements.
Qualifications & Skills:
• Proven experience in a production management or similar leadership role.
• Strong organizational, planning, and time management skills.
• Ability to manage and motivate a diverse team across multiple departments.
• Familiarity with production processes, capacity planning, and continuous improvement strategies.
• Excellent communication skills, with the ability to build relationships with customers, suppliers, and team members.
• Strong problem-solving skills with a focus on process improvement.
• Proficiency in Microsoft Office Suite and experience with project management or scheduling software.
• Knowledge of HR policies and procedures is preferred.
If you are interested in applying for the role and think you have what it takes to join our dynamic team, please email a copy of your CV along with your supporting cover letter to our HR department:
--------------------------------------------------------------------------------------------
Sales Executive
Closing date: 01st December 2024
Overview
We are seeking a motivated and results-driven Sales Executive to join our dynamic team. As a Sales Executive, you will play a key role in driving the growth of our business by identifying and closing new sales opportunities, building strong client relationships, and maintaining a high level of customer satisfaction.
Key Responsibilities:
1. Lead Generation: Identify and generate new sales leads through various channels such as tradeshows, networking, cold calling, and market research. Client Engagement: Build and maintain strong, long-lasting relationships with clients, understanding their needs, and providing tailored solutions, including hosting Clients within a hospitality setting.
2. Sales Presentations: Deliver compelling presentations and product demonstrations to potential clients, positioning BAMD at the forefront of future projects, before they go to quote. Negotiation and Closing: Skillfully negotiate contracts and pricing with potential clients, managing the sales cycle from initial contact to deal closure.
3. Account Management: Maintain relationships with existing clients, ensuring a high level of customer satisfaction and identifying opportunities for upselling or cross-selling.
4. Sales Targets: Meet or exceed monthly, quarterly, and annual sales goals and KPIs as set by the Board.
5. Market Research: Stay informed about industry trends, market conditions, and competitor activities to identify opportunities for growth and improvement.
6. Reporting: Prepare and submit regular sales reports, providing insights on sales activities, opportunities, and forecasts.
Qualifications & Skills:
• Bachelor’s degree in business, Marketing, or related field (preferred but not required).
• Proven experience as a Sales Executive or in a similar sales role.
• Excellent communication, negotiation, and interpersonal skills.
• Ability to work independently and in a team environment.
• Strong organizational skills and attention to detail.
• Proficiency in CRM software and Microsoft Office Suite.
• Results-oriented with a proven track record of meeting or exceeding sales targets.
• A full UK Driving license.
• The role will require travel and overnight stays.
If you are interested in applying for the role and think you have what it takes to join our dynamic team, please email a copy of your CV along with your supporting cover letter to our HR department:
--------------------------------------------------------------------------------------
Bamd Ltd – Investment Readiness Consultancy Public Tender
Published Date – 26/04/2021
Bamd Ltd are looking for a supplier for carry out the below services, We are looking to select one supplier to award this contract to. We are looking for a supplier who has proven knowledge within the Automotive or Composites sectors.
Instructions for this Tender
-
All questions are to be provided via email to sam@bamd.co.uk no later than 5pm on 03/05/2021
-
All formal quotations to be submitted via email to sam@bamd.co.uk no later than 5pm on 10/05/2021
-
Once submitted all suppliers will be scored based on an internal matrix of BAMD Ltd specific criteria
-
All suppliers will be notified once we have nominated
-
Sales Agreement will then be issued to the successful supplier
-
The maximum budget for this procured service is £50,000 excluding VAT
Supplier Scoring System;
Costs
Scored from 0-5
33% of Final Score
Lead time
Scored from 0-5
33% of Final Score
Previous Industry Experience
Scored from 0-5
33% of Final Score
Project Scope – 12 month consultancy project regarding achieving Investment Readiness of BAMD Ltd based on the 4 below deliverables
Quotation format – Please quote either a day rate and days required to deliver the below or a fixed price
Deliverables;
-
Investment Deck & Financial Model
-
Executive summary highlighting the company’s business proposition and investment potential
-
Details of the company’s management team, track records, roles/responsibilities & value-add to business
-
Private or Public investment analysis
-
Operational infrastructure readiness
-
-
Business Plan
-
Existing business plan analysis
-
3 year future growth business plan and implementation
-
Support to build an investment ready management team and identify GAP analysis
-
Notes:
-
The Busines Plan to include Summary, Profit & Loss, Balance Sheet, Cashflow and Discounted Cashflow (for valuation purposes)
-
Competitors & Market Research
-
Competitors Analysis
-
New Sector/Opportunities research/analysis
-
-
Financials
-
Cash flow projections
-
Investment GAP Analysis
-
SWOT analysis of current financial position
-
Additional Notes to the Tender – contracted party will support the following to achieve the above remit:
-
an executive summary highlighting the Company’s business proposition and investment potential – collaborative between FTL & EAV.
-
details of the Company’s management team, their track record, their roles/responsibilities and their value-add to the business
-
details/analysis of the Company’s product/service proposition
-
market and competitor analysis, and go-to-market strategy
-
operational infrastructure
-
financial analysis
-
investment analysis
-
risk analysis
-
plan of execution (this will be summarised from the more detailed actions identified for us and the Company’s management team).
Supplementary Appendix:
To assist and identify suitable investors/financiers to address the Company’s funding requirements. Such investors/financiers will include inter alia:
-
(i) private/public investment funds from our network
-
(ii) investors connected with our network of wealth management funds
-
(iii) high net worth individuals who may express an interest in investment in the green-tech sector
-
(iv) funds focused specifically in the green-tech sector
-
(v) banks and entities focused on debt-led financing
To assist and prepare presentations, participate with Q&As and address requests for other financial information and analysis solicited by any potential investor/financier.
Additionally, your remit will include:
-
(a) providing guidance to the management team on all aspects of the strategic, commercial, operational and financial performance of the Company and advice on actions to improve results;
-
(b) review of existing contractual arrangements and assisting in improving the contractual terms to drive better financial performance for the Company;
-
(c) managing stakeholder expectations, particularly in respect of investors, banks and other institutions and individuals with a vested interest in the performance of the company; and,
-
(d) identifying and managing risk in conjunction with the directors of the Company.


come and meet us
Want to join the team? Why not come and see and meet the team, facility and atmosphere within BAMD